Concrete materials have been traditionally used to construct buildings for a long time. However, technological advancements have prompted the construction industry to adopt composite materials with enhanced thermal and mechanical resistance properties.
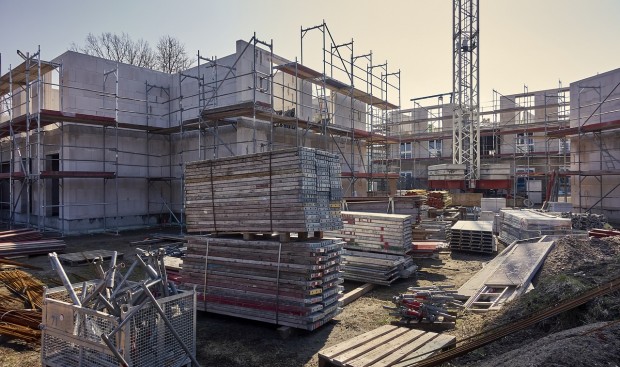
What is a Composite Materials?
Combining two substances with distinct physical and chemical properties forms a composite material. They unite to produce a specialized material for a specific task, such as being more robust, lighter, or resistant to electricity. Additionally, they can enhance both strength and stiffness. These materials are preferred over traditional materials since they enhance the qualities of the materials that they are based on and may be utilized in a greater variety of contexts.
Moreover, the urgent need for composite materials is becoming more critical in light of the increasing severity of environmental issues. To help combat the effects of global warming, composite materials will reportedly need to be more resilient in various weather conditions, and the ecological impact of continually renewing infrastructure is expensive.
As mentioned, reinforcing concrete with steel bars can be done in various combinations. These arrangements can include using thicker or thinner bars of different or the same length and stacked in parallel, lattice, or randomly oriented. Thus, depending on their particular role, other composite materials of varying constructions might acquire one of these distinct characteristics.
On the other hand, when it comes to construction, the essential characteristics of composite materials are their tensile or compressive stiffness, their resilience to fire, their fatigue life, their resistance to vibration and harmonic load, their joinability, and, depending on the application, their chemical resistance.
In Saudi Arabia, a concrete flood channel that is 23 kilometers long has been strengthened with corrosion-resistant materials such as glass-fiber reinforced polymers (GFRP), which have been employed as replacements for steel as support for concrete. Additionally, strength and resistance to high temperatures are characteristics of carbon fiber-reinforced polymer (CFRP) and GFRP; CFRP is mildly more durable and impervious to high temperatures but comes at a higher price.
By incorporating nanoparticles or new elements, manipulating the microstructure, employing powder metallurgy, and other techniques, it is possible to increase the strength of the ceramic matrix.
Also Read: Earthquake Resistant Buildings: How Are These Structures Made to Withstand Disasters?
Benefits of Using Composite Materials
Design Flexibility
Composites made of thermoset materials provide designers with practically unrestricted versatility in developing shapes and forms. They can be shaped into the most intricate components and manufactured in various densities and chemical compositions to achieve specific performance characteristics.
Improved productivity
When multiple components assembled in the past are combined into a single component, industrial designers and engineers can cut the expenses associated with assembly. Post-processing is also unnecessary because inserts can be molded directly into the component during molding. At the same time, additional machining is typically unnecessary when working with composites, decreasing work-in-process and time-to-market.
Low cost per cubic inch
Thermostat composites exceed conventional materials like wood, engineered thermoplastics, and metals in terms of material costs when compared on a volumetric basis. Furthermore, since thermoset composites contain a relatively low amount of petroleum, they are not affected by the price swings seen in items derived from petroleum production.
Lower material costs
The minimal wastage and reduced material costs compared to metal products result from the precise molding that thermoset composites enable.
Related Article: US Construction Spending Soars Despite Decline in Public Projects